1000L/H to 6000L/H Liquid Gas Carbonated Drink Carbon Dioxide Single Mixer Co2
- $5000.00 / 1 - 1 sets
$500.00 / >=2 sets - 1 set
- Zhangjiagang City Bottling Machinery Co., Ltd.
- Jiangsu, China
- Mr Phil Lane
PRODUCT DETAIL
payment terms: | L/C,Western Union,D/P,D/A,T/T,MoneyGram | Model 2: | Double Tank Carbonator |
Core Components Warranty: | 1 year | weight: | 1000kg |
Video external inspection: | if | Model 4: | High Ratio 5 Tank Carbonator |
Mechanical test report: | if | Name 3: | carbonated |
Material: | SUS304, SUS316 | Applicable industries: | Hotels, Manufacturing Plants, Food and Beverage Plants, Farms, Restaurants, Retail, Food Stores, Energy and Mining, Food and Beverage Stores |
Dimensions (L*W*H): | custom made | Supply capacity: | 15 sets per month |
capacity: | 500LPH-10000LPH | port: | Shanghai Port or Ningbo Port |
Health status: | new | Voltage: | custom made |
Name 2: | CO2 mixer | strength: | custom made |
Model 1: | Single Tank Carbonator | product name: | CO2 Beverage Blender |
Warranty: | 1 year | Processing Type: | Carbonated drinks |
Marketing Type: | New Products 2020 | Processing: | mixer |
Packaging Details: | Seaworthy packaging | brand: | bottling |
Showroom location: | not any | place of origin; place of origin: | Jiangsu |
application: | Mixing carbon dioxide into beverages | Model 3: | Three Tank Carbonator |
Core components: | Bearings, motors, pressure vessels |
Product Description
1. Single-tank carbonator/CO2 mixer
Working principle: The beverage is pressurized to a static mixing rod by a high-pressure pump, then mixed with carbon dioxide gas, and finally enters the mixing tank for secondary mixing to increase the mixing effect, thereby completing the carbonated beverage. Features: 1. Exquisite materials and precise processing: all contact parts are made of high-quality stainless steel, fully polished inside and outside, in line with international beverage machinery standards; 2. Automatic operation, stable equipment: electronic control throughout the process; alarm device works when a fault occurs; 3 , Easy to operate, easy to adjust When operating, just press the prescribed program to open the button, and it can run normally. The production capacity and mixing ratio of the beverage can be easily adjusted through the operating valve on the machine. 4. The mixing is uniform and the proportion is accurate. The flow meter and manual valve are used to control and adjust the proportion of liquid and CO2. 5. Healthy structure and easy to clean The machine adopts a stainless steel closed system, installs CIP balls to connect the essence cleaning equipment, cleans the equipment and pipes with acid, alkali and hot water, and then ensures that the beverages made by the machine can meet the hygienic requirements.
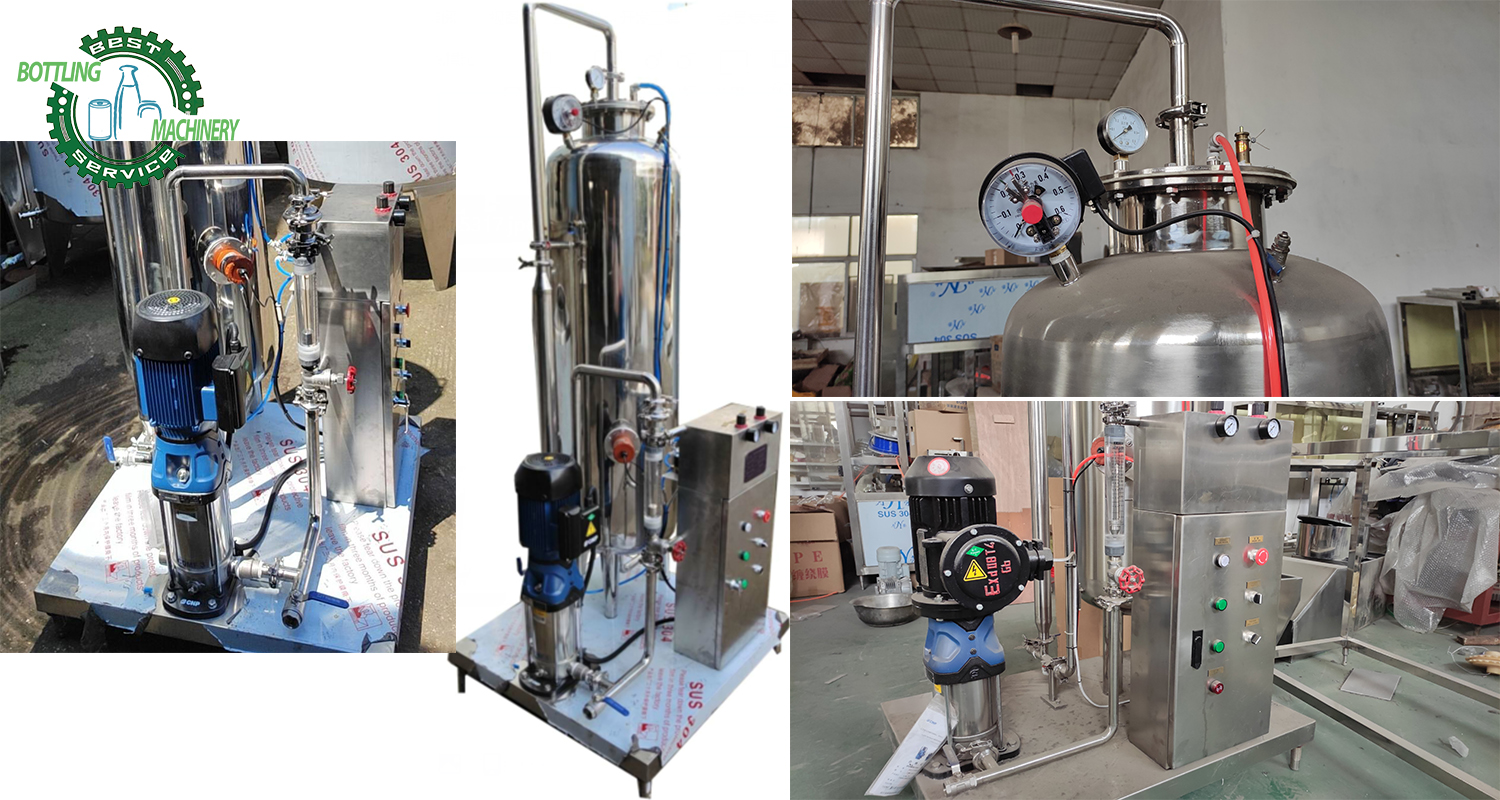
capacity: | 1000L/H | 2000L/H | 3000L/H | 4000L/H | 5000L/H | 6000L/H | |||||
Gas content: | Virtual Reality 2.5 | ||||||||||
Beverage inlet temperature: | 0-5℃ | ||||||||||
Working pressure of mixing tank: | 0.2-0.5Mpa | ||||||||||
Compressed air consumption: | 2.5m³/h | 5 cubic meters/hour | 7.5m³/h | 10m³/h | 12.5m³/h | 15 cubic meters/hour | |||||
strength: | 0.75KW | 1.5KW | 2.2KW | 3KW | 3KW | 4.5KW | |||||
Mixing tank D*H(mm) | 400*1500 | 400*1500 | 420*1500 | 450*1500 | 450*1500 | 550*1500 | |||||
Dimensions (mm): | 1100*900*2200 | 1200*1100*2200 | |||||||||
Weight (kg): | 400 | 420 | 500 | 520 | 550 | 600 |
2. Double tank carbonator/CO2 mixer
1. Exquisite materials and precise processing: All contact parts are made of high-quality stainless steel, fully polished inside and outside, in line with international beverage machinery standards; 2. Automatic operation, stable equipment: electronic control of the whole process; alarm device works when a fault occurs; 3. Operation Convenient, easy to adjust and easy to operate, just press the prescribed program to open the button, and it can run normally. The production capacity and mixing ratio of the beverage can be easily adjusted through the operating valve on the machine. 4. The mixing is uniform and the proportion is accurate. The flow meter and manual valve are used to control and adjust the proportion of liquid and CO2. 5. Healthy structure and easy to clean The machine adopts a stainless steel closed system, installs CIP balls to connect the essence cleaning equipment, cleans the equipment and pipes with acid, alkali and hot water, and then ensures that the beverages made by the machine can meet the hygienic requirements. 6. High-ratio carbonation uses a degasser to take away the oxygen in the beverage before CO2 mixing; it provides more space for carbon dioxide mixing; adopts a plate heat exchanger, which can be reduced by a cold source before direct mixing Beverage temperature, reduce the temperature rise on the way, and obtain better gas mixing effect;
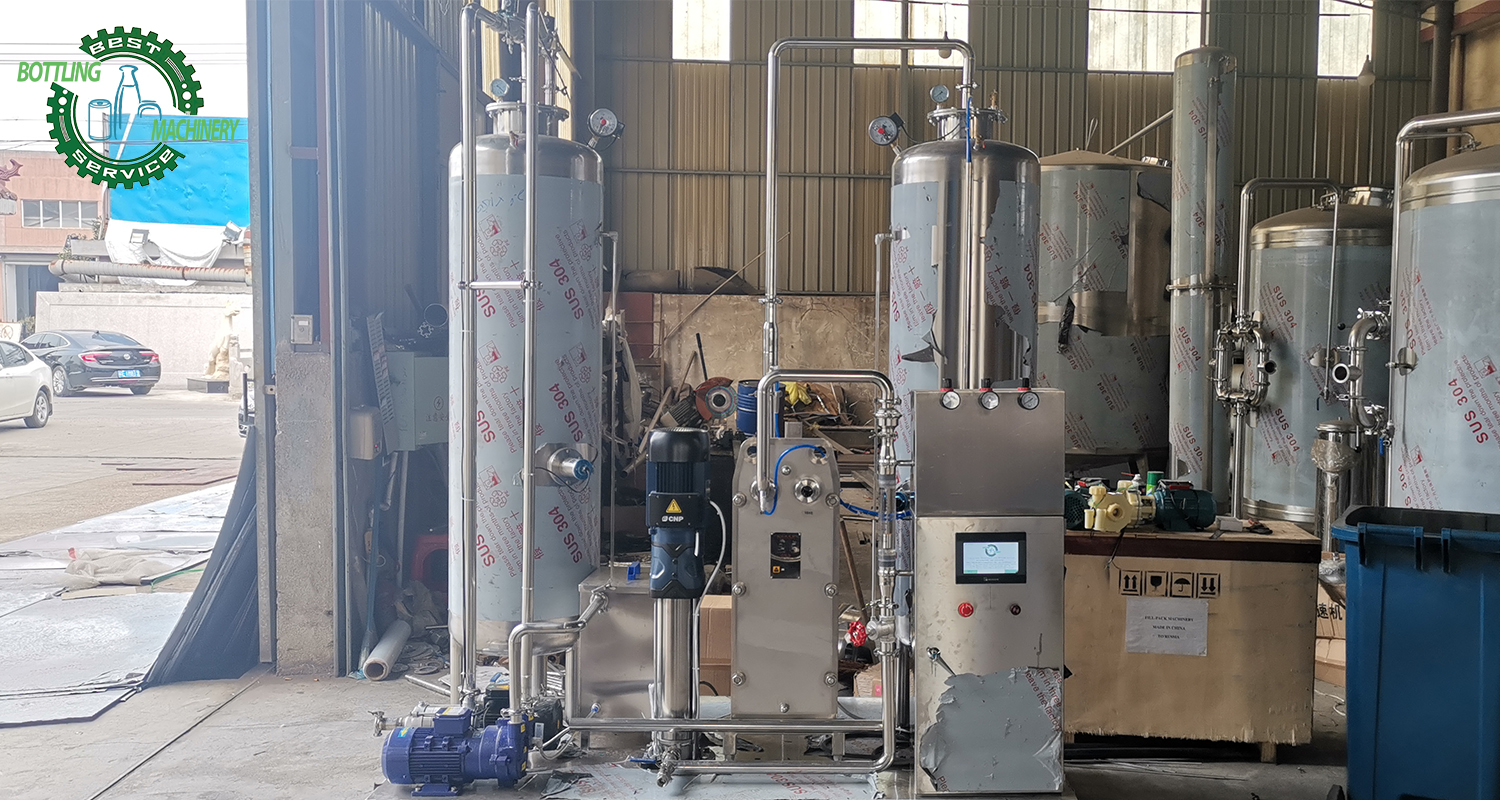
capacity: | 1000L/H | 2000L/H | 3000L/H | 4000L/H | 5000L/H | 6000L/H | |||||
Gas content: | virtual reality 4 | ||||||||||
Beverage inlet temperature: | 0-5℃ | ||||||||||
Working pressure of mixing tank: | 0.2-0.5Mpa | ||||||||||
Compressed air consumption: | 4 cubic meters/hour | 8 cubic meters/hour | 12 cubic meters/hour | 16 cubic meters/hour | 20m³/h | 24 cubic meters/hour | |||||
strength: | 3.5KW | 3KW | 3.7KW | 4.5KW | 4.5KW | 6KW | |||||
Degassing tank D*H(mm) | 400*1500 | 400*1500 | 420*1500 | 450*1500 | 450*1500 | 550*1500 | |||||
Mixing tank D*H(mm) | 400*1500 | 400*1500 | 420*1500 | 450*1500 | 450*1500 | 550*1500 | |||||
Dimensions (mm): | 1400*1200*2500 | 1500*1400*2500 | |||||||||
Weight (kg): | 480 | 500 | 580 | 600 | 630 | 680 |
Product structure and working procedures:
1. CO2 tank, syrup tank, liquid level device, static mixing device, tank body, electrical control system, gas supply tank, and necessary production pipelines and cleaning pipelines, including ball valves, solenoid valves, and check valves. (See Figure 1: Main Structure) 2. Main Workflow a. Cooling water→multi-stage pump→oxygenated CO2→capacity control b. Cooling syrup → multi-stage pump → syrup tank → volume control (a and b → multi-stage pump → static mixing device → c.CO2 gas source → filter decompression → tank → filling machine
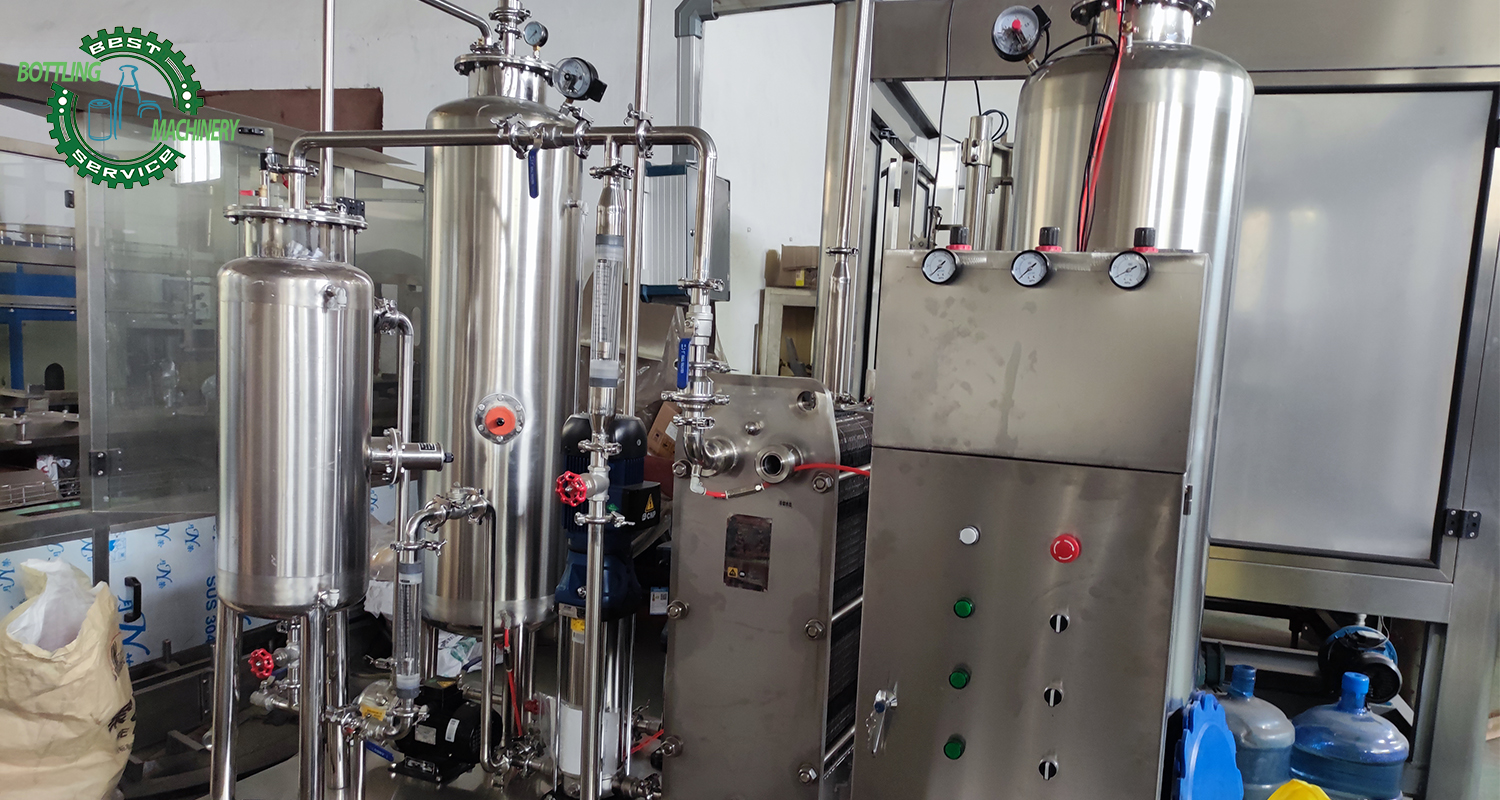
3. High ratio 5-tank carbonator/CO2blender
1. Provide degassing, mass flow mixing of syrup and water, bicarbonate. All pressure vessels are designed, manufactured and tested in accordance with the applicable provisions of the ISPESL Code (Standard). 2. A degassing system that removes air to a low level (1ppm residual oxygen) for stable foam-free filling. The system consists of a stainless steel degassing tank consisting of a vacuum pump, into which water is sprayed as a fine mist in a carbon dioxide atmosphere. 3. A proportioner provides fully automatic control of the mixing of two streams of running water/syrup. Flow control is recipe based. The system includes the following quality components: 4. A syrup tank equipped with a liquid level control system, and a flow meter for the quality of the syrup to ensure the tightness of mixing and repeatable operations. Two control valves are used to regulate the flow of syrup from the test results. 5. Two centrifugal mixing pumps and a linear carbonation injection control system to maintain +/- 0.02 vol/vol carbonation control. This range is maintained by measuring the CO2 flow in a CO2 mass flow meter and controlling it at a rate proportional to the product flow through a regulating valve. 6. 1 buffer tank with capacitive liquid level control, which controls the system flow according to the formula reflected by the liquid level of the finished product in the tank. The capacitive liquid level probe system provides continuous liquid level indication to the PLC for fine-tuning and adjustment of mixer flow. The finished product is discharged to the filling machine. 7. A control package provides an automation system for precise process mixing control. The kit includes a suitable PLC, control program, video graphic operator interface with information and control screens, and all necessary process sensors and safety devices. System software includes system schematics, recipe manager, production displays, trends, alarm screens with full security password protection. 8. A control panel, made of stainless steel, with PLC; electrical switches; relays; and control of the flow meter system. The color touch screen operation interface is installed on the front of the panel. The panel door is equipped with a safety electrical disconnect latch and the door is sealed. 9. A pneumatic unit, including: all air valves, air switches and air pipes, and a tubular stainless steel base to mount most components. The base is of welded construction and includes adjustable stainless steel legs and HDPE mounting pads.
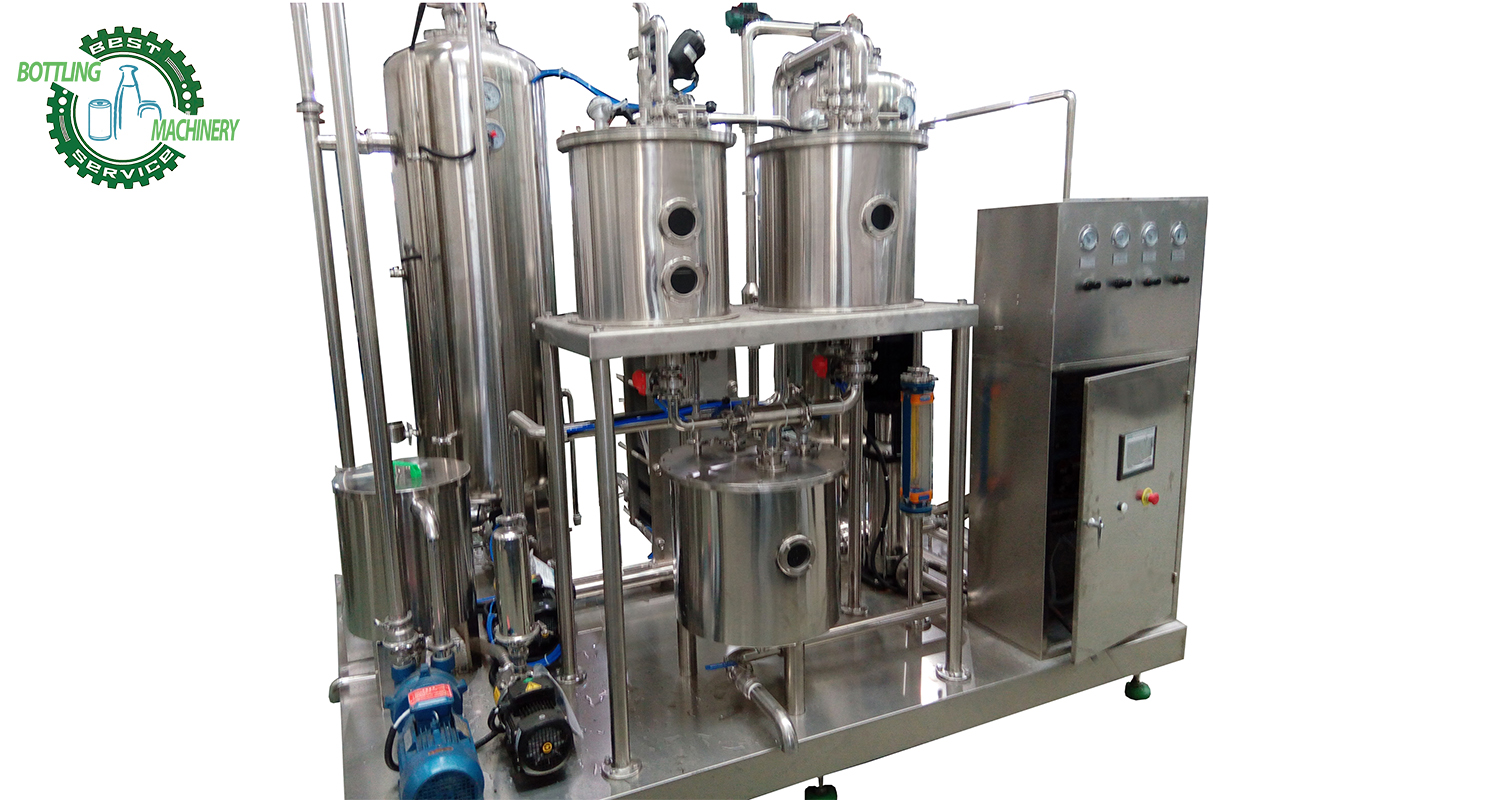
capacity: | 4000L/H | 5000L/H | 6000L/H | ||
Gas content: | >VR 4.0 | ||||
Beverage inlet temperature: | 0-4℃ | ||||
Working pressure of mixing tank: | 0.2-0.5Mpa | ||||
Compressed air consumption: | 0.2 m3/min | ||||
Compressed air pressure: | 0.6MPA | ||||
water/syrup mix | 3:1—6:1 | ||||
strength: | 5KW | 5.5KW | 6KW | ||
Mixing tank (including pipe and table height) D*H(mm) | 500*2100 | 500*2100 | 500*2100 | ||
Dimensions (mm): | 1000*1200*2100 | ||||
Weight (kg): | 800 | 820 | 850 |
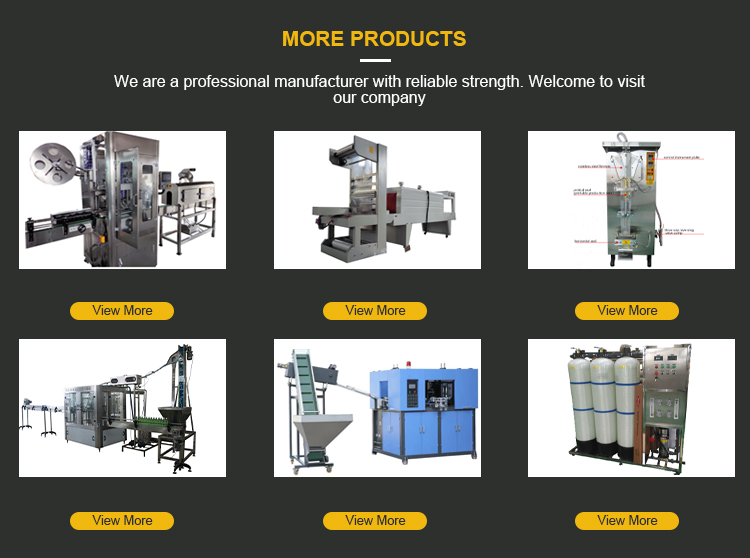
VIEW MORE
YOU MAY LIKE
Other Products
-
Semi-automatic stainless steel 304 turntable collection glass bottle sorting sorting table machine$500.00 - $700.00 / set
-
Carbonated lemon juice wine automatic SUS304 water spray PET plastic bottle insulation machine$500.00 - $15000.00 / set
-
Semi automatic small 2000bph rotary beer wine glass bottle 24 head water jet washing machine with heater$500.00 - $790.00 / set