Customized filter cage 316L 304SS carbon steel material 135mm*6m 16 wire 4mm with venturi for bag filter matching filter bag
- $18.90 / 50 - 199 pieces
$16.50 / 200 - 999 pieces
$11.30 / >=1000 pieces - 50 pieces
- Shanghai Aasf Technology Co., Ltd.
- Shanghai, China
- Mr fionafu
PRODUCT DETAIL
Local Service Location: | Canada,United States,Italy,France,Germany,Pakistan,India,Thailand,Malaysia,Australia,Nigeria; | Packaging Detail: | Iron crate with water proof; |
Temperature ranges: | 100-140T 140-180T 180-220T 240 T; | Showroom Location: | United States,Italy,France,Germany,Pakistan,Thailand,Malaysia,Australia; |
Top design: | With top tube and venturi; | After Warranty Service: | Online support,Spare parts; |
Brand Name: | AASF; | Video outgoing-inspection: | Provided; |
Warranty: | 6 months; | Size: | 135mm*6m; |
Package Preview: | ; | Product name: | Filter cage; |
Core Components: | Engine,carbon steel,316L,304SS; | Applicable Industries: | Garment Shops,Building Material Shops,Manufacturing Plant,Machinery Repair Shops,Farms,Construction works ,Energy & Mining,Other; |
Place of Origin: | Shanghai, China; | Thickness: | 4 mm; |
Treatment: | smooth surface; | Condition: | New; |
Machinery Test Report: | Not Available; | Rod number: | 16 wires; |
Port: | Shanghai; | Payment Terms: | D/P,D/A,T/T; |
Marketing Type: | New Product 2020; | Warranty of core components: | 1 Year; |
Bottom design: | Roud; | Working condition: | To match filter bags; |
Materials Options: | 316L 304SS carbon steel materialmaterial; |
Product Description
Filter Cage constructions typically consist of 10, 12 or 20 vertical wires. The horizontal ring spacing on the cage can be 4″, 6″ or 8″. If plenum height restrictions are a problem, two piece cages are available in popular “twist-lock” or “fingers” styles. For areas where moisture or acid corrosion present we can provide a range of materials, often galvanized steel or stainless steel. Top load baghouse cages are available with a T-flange, ring top or several styles of rolled flange tops. Cage diameters range from 4″ to 6 1/8″. Wire thickness ranges are; 9 gauge, 10 gauge and 11 gauge. Cages for bottom load baghouses are constructed with a split collar or split ring top. Cage diameters range from 4″ to 6 1/8″. Wire thickness ranges are 9 gauge, 10 gauge and 11 gauge.
For more efficient cleaning, Venturi are available for all diameter cages. Venturi come in 3″ to 6″ lengths. Venturi are made in a variety of materials including; aluminum, carbon steel, galvanized and stainless steel.
Our dust collector cages can be made to fit existing collectors from any baghouse manufactures such as , Mikropul, Wheelabrator, Masterjaya, Filtercorp, etc. We can also manufacture uncommon and specialized cage designs as required.
Rolled flange (or Turned Down Flange) and venturi for top load units (Back Row)
Split collar ( or Rolled Band) for bottom load unit (Front Row)
Materials/Finishes
Carbon Steel/Mild Steel
Galvanized Steel
304 Stainless Steel
316 Stainless Steel
Epoxy Coated (High Temp <325°)
Inconnel 600 or 601
Vertical Wires and Wire Gauges
10, 12, and 20 vertical wires most common
5, 6, 8, 16 and 24 also available
10, 11, and 12 gauge wire most common
7, 9, and 13 also available
Sizes
Common diameters: 4″ – 6-1/8″ (fits most baghouse OEMs)
Common lengths: 6′ – 12′ (shorter/longer lengths also available)
Cage Shape
Round (most common)
Oval
Envelope
Cage Top Styles
Rolled Flange (Turned Down Flange) – Most Common Top Load Style
Split Collar (Rolled Band) – Most Common Bottom Load Style
Slotted
All Wire
Split Ring
Cage Bottom Styles
Welded – Most Common
Crimped
Snap
Wire Formed
Additional Options
Venturi
Aluminum, carbon steel, galvanized or stainless steel
Attached (riveted) or drop-in/removable designs
3″ – 6″ lengths
Two-piece option
“Twist-lok” style (good for baghouses with low clearance)
“Fingers” style
Slide Lock
Learn More about Baghouse Cages on Our Blog
WHICH BAGHOUSE HOPPER DISCHARGE METHOD IS BEST?
Many problems arise over how to properly dispose of dust in the baghouse once it is collected. Improper dust disposal can directly impact the operation of your baghouse. Storing dust in your baghouse hopper is a terrible idea. Dust collector…
FAQS - DUST COLLECTION SYSTEM DESIGN AND OPERATION
Question: What is "normal" differential pressure in a baghouse? Answer: In most applications a baghouse dust collector should run between between 3" to 6" w.g. under normal use. Once levels rise above 6" (roughly) and the cleaning system…
FAQS - DUST COLLECTOR FILTERS
Question: Why are my baghouse filters so expensive to replace? Answer: Many simply buy their replacement filters from the OEM or sales rep that supplied their baghouse. Often times, manufacturers and sales rep organizations deliberately sell…
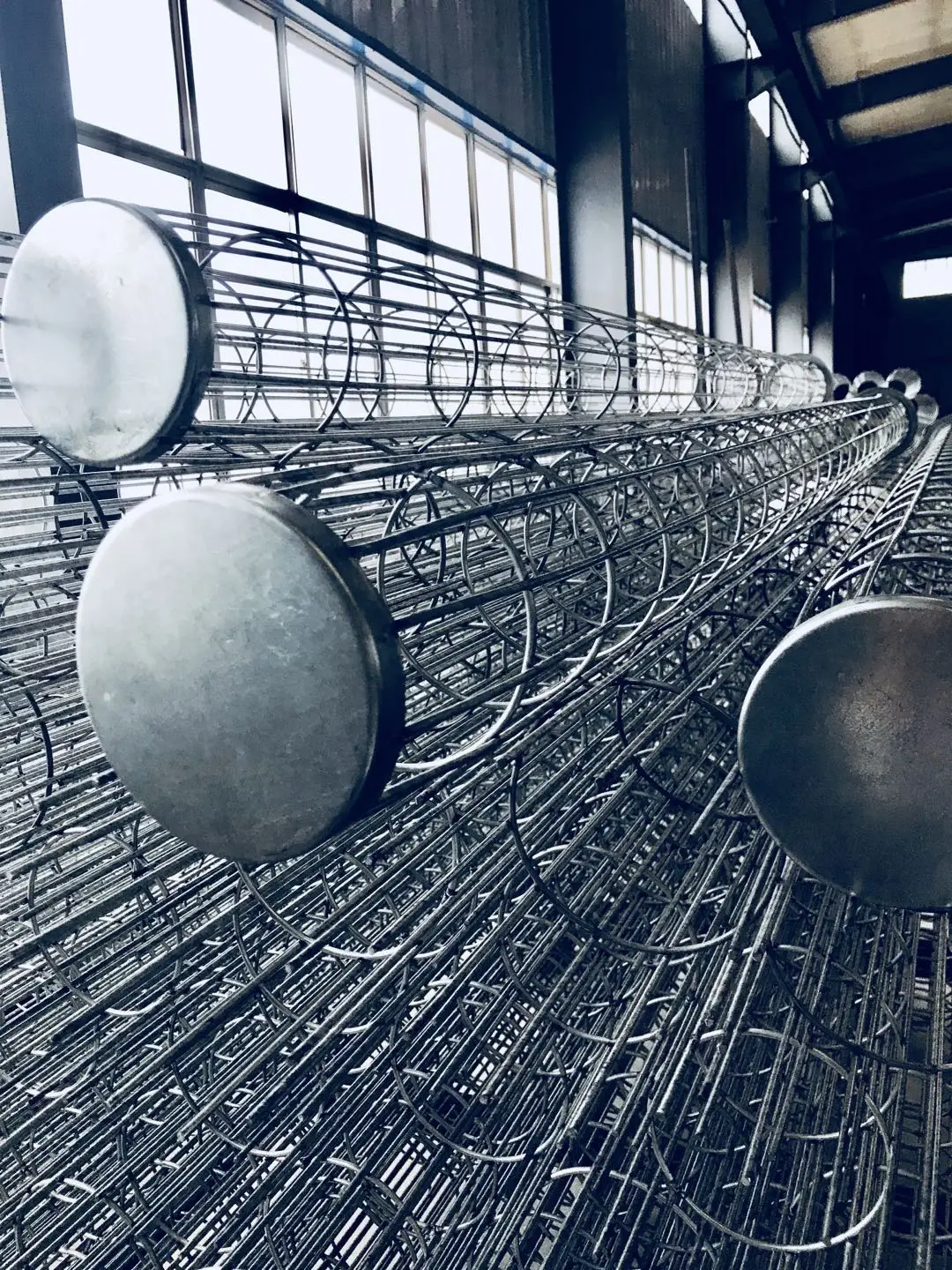
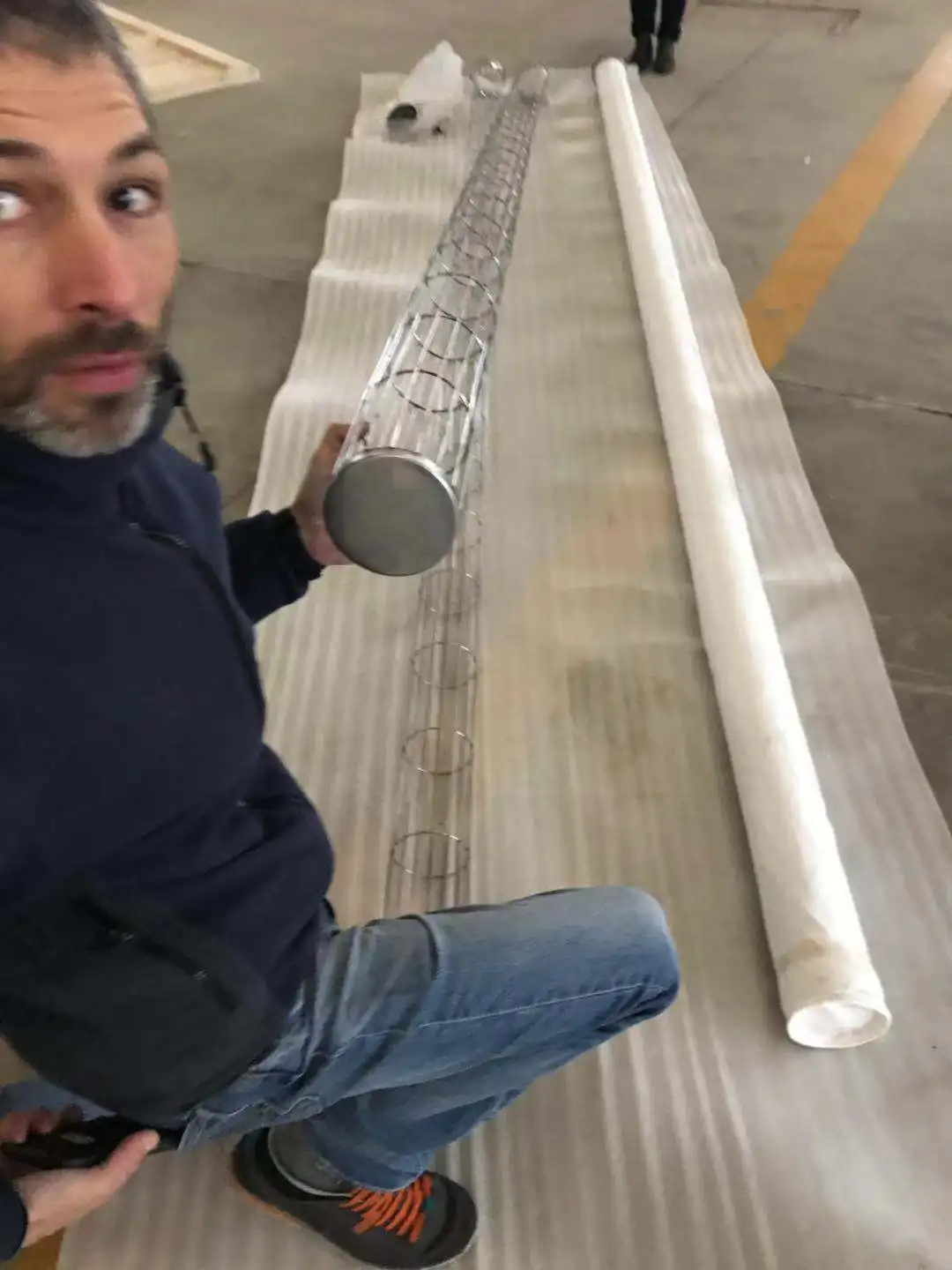
Related Products
Company Introduction
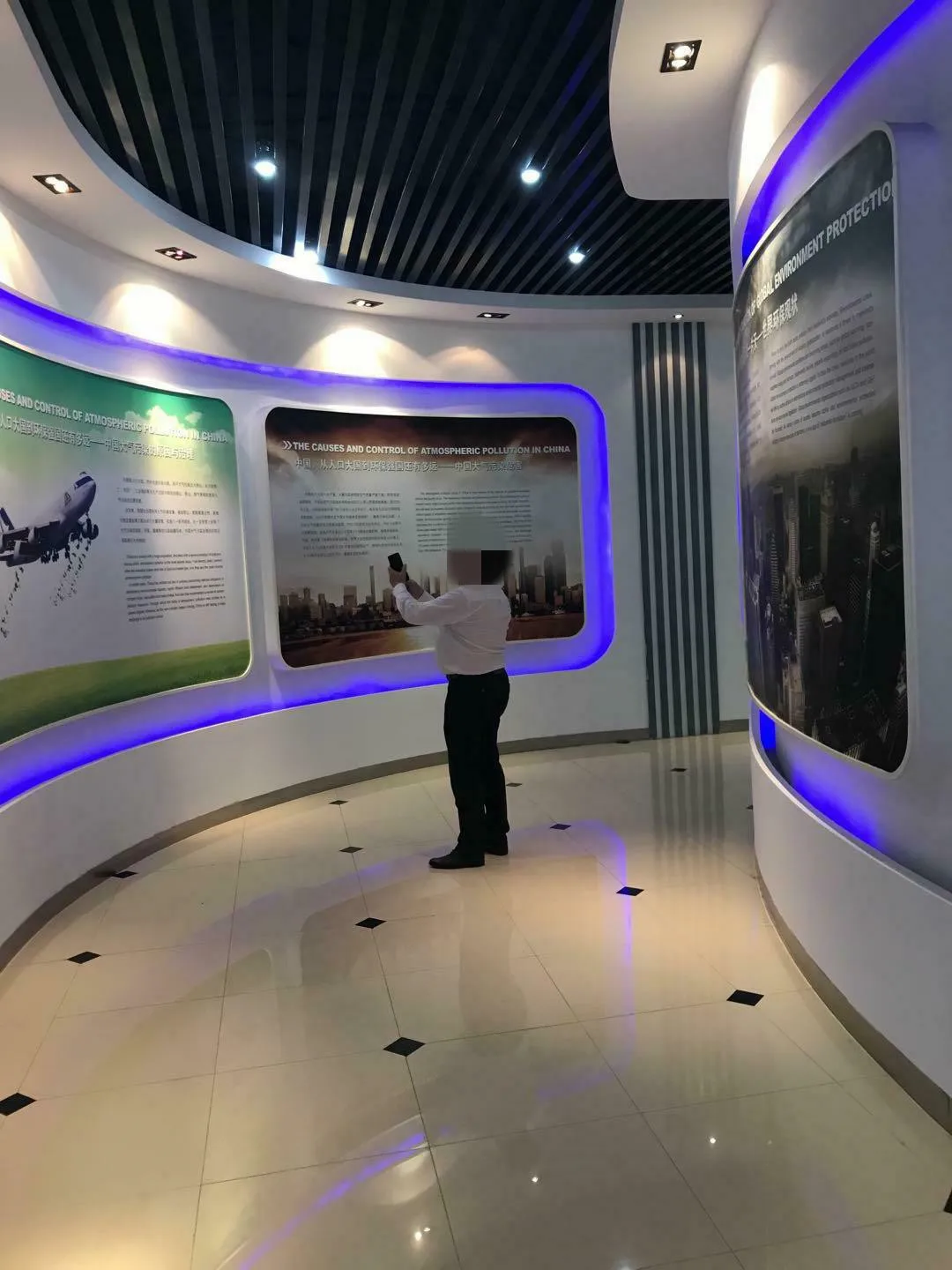
SHANGHAI AASF TECHNOLOGY CO., LTD
AASF as specialist who is manufacturing and supplying standardized &customized products with full ranges, filter bag, filter cage, solenoid valve, diaphragm kits, connectors etc. It has office in Shanghhai and Hongkong where is convenient to offer customers best service, gaining profound reputation with excellent professional abilities and wild connections in China. AASF has full profound STPJ brand in domestic market . The expertise of AASF is pertaining to industries in the field of steel manufacturing, cement, energy, petroleum and environmental equipment, environmental and harmonious welding equipment, healthy and sustainable machine equipment for better environment, offering high quality facilities and components.
AASF Shanghai registered capitals is 5million since 2017 with over 30 years professional filtrational experience. Our sales increased dramatically with good reputation, 90% overseas, 10% domestic sales.Our goal is to to build International Brand, creating top quality, at your best service.
Should you have any questions, please feel free to contact us.
filter bag manufacturing
filter bag process
filter bag stich
Filter bag production 1
Filter bag production 2
Pulse valve production workshop 1
Pulse valve production workshop 2
Pulse valve production workshop 3
Certifications
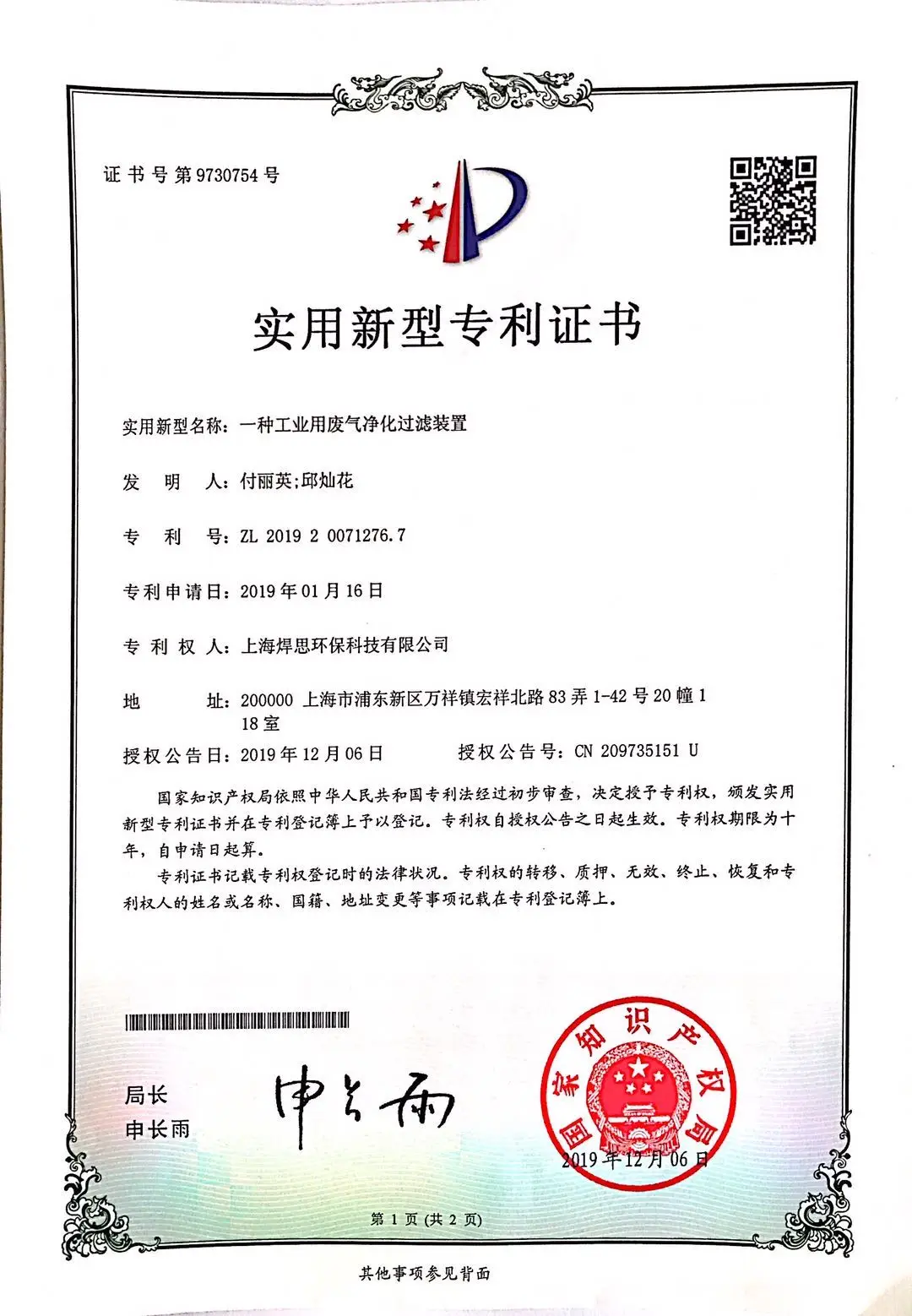
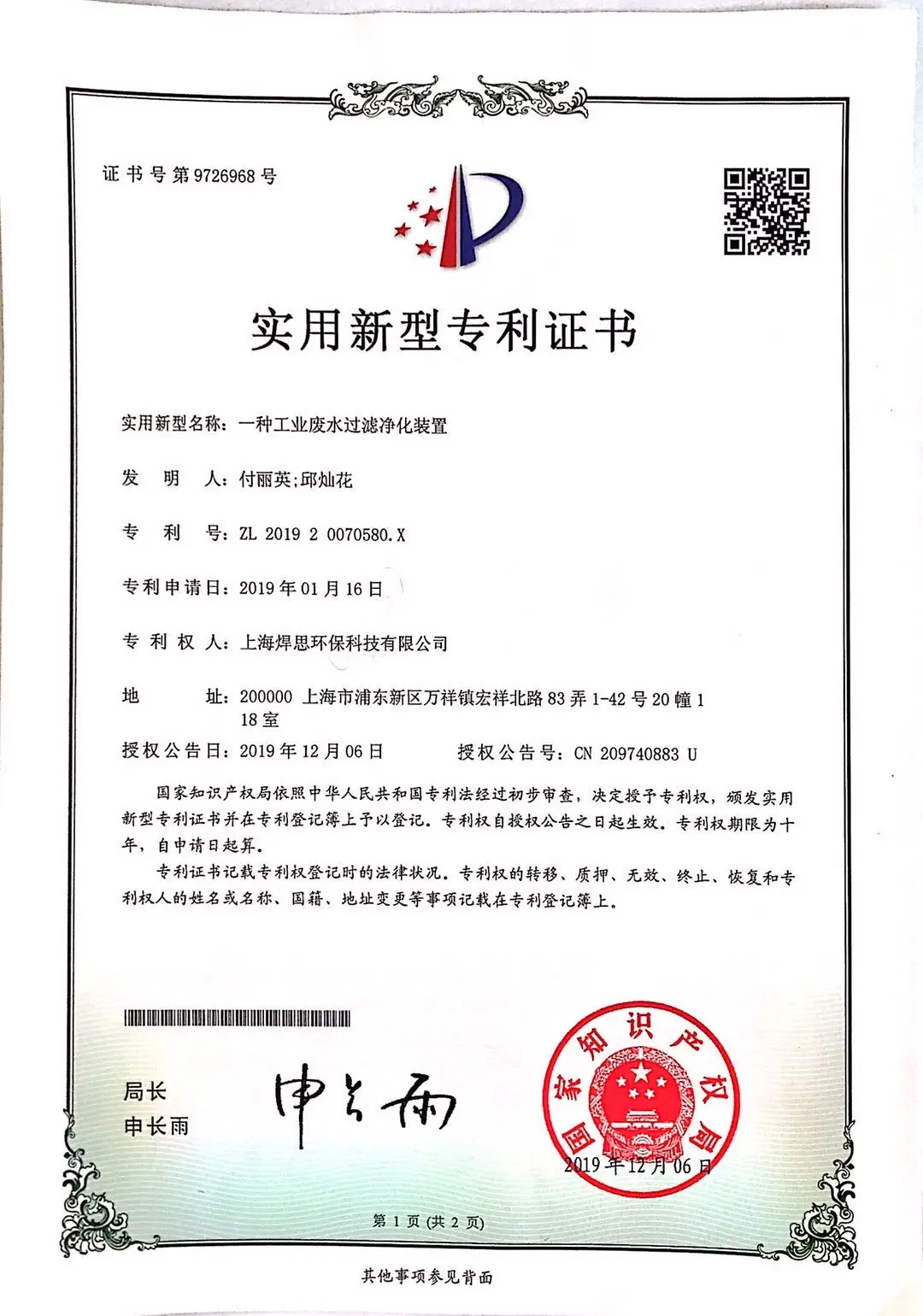
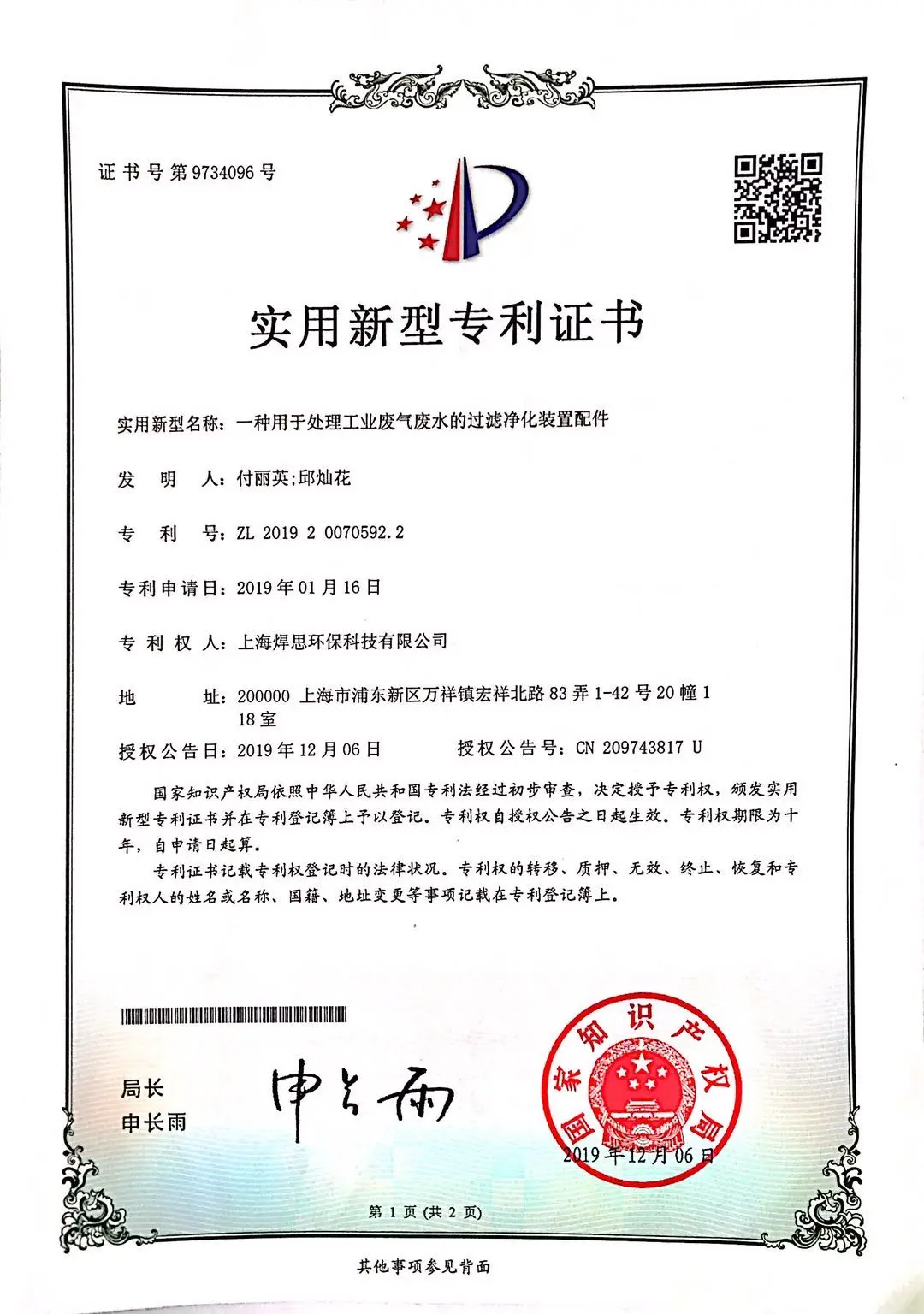
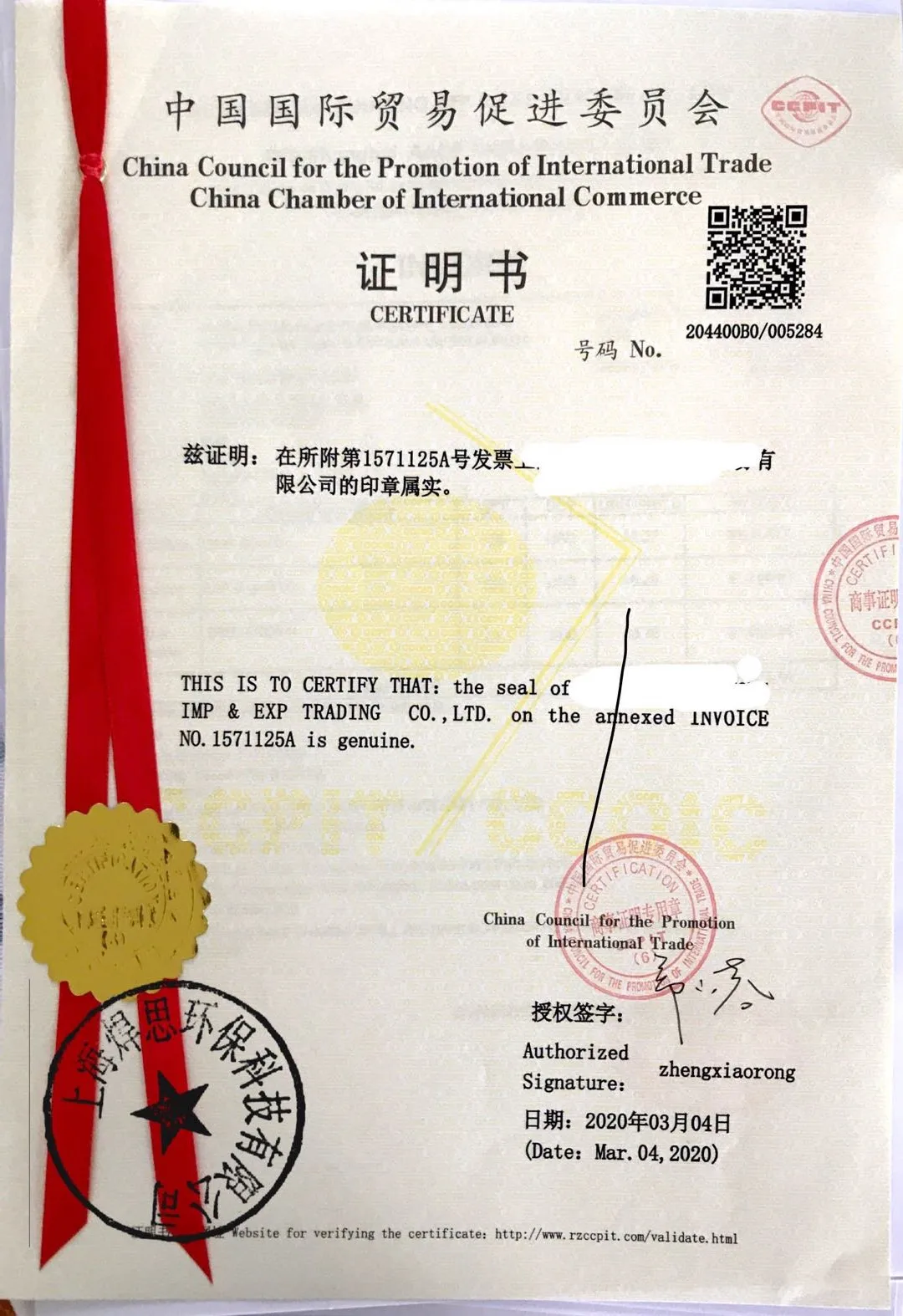
Application
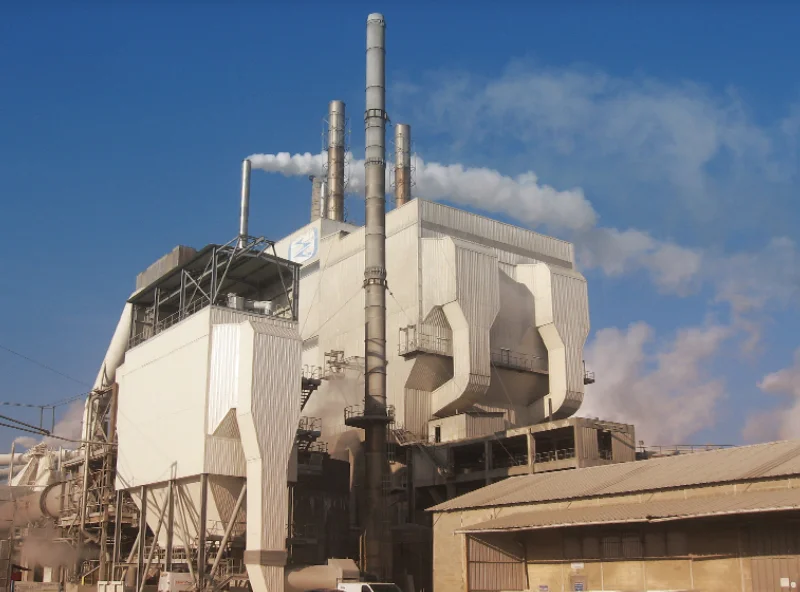
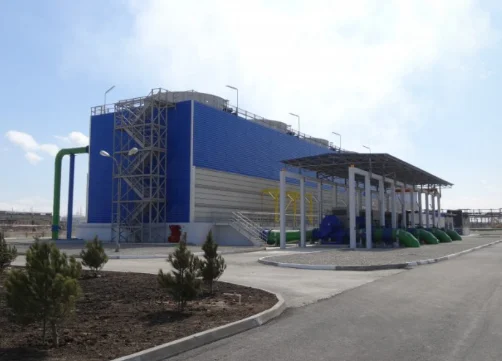
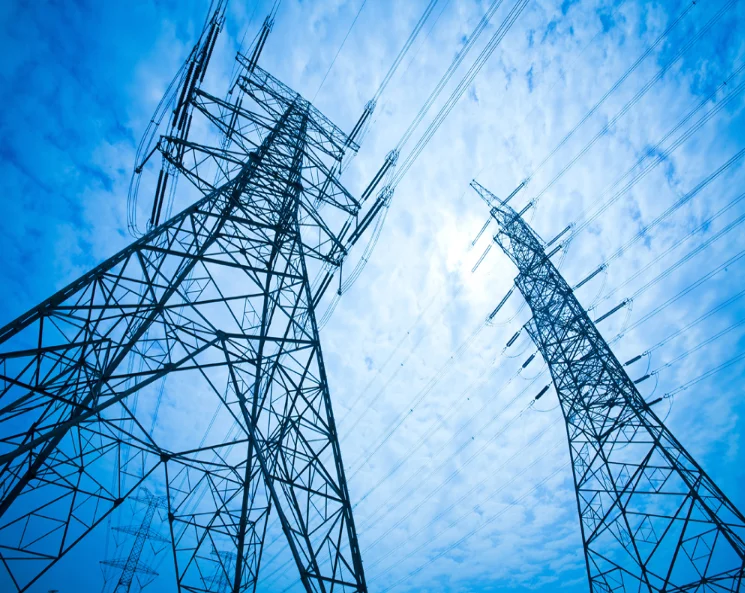
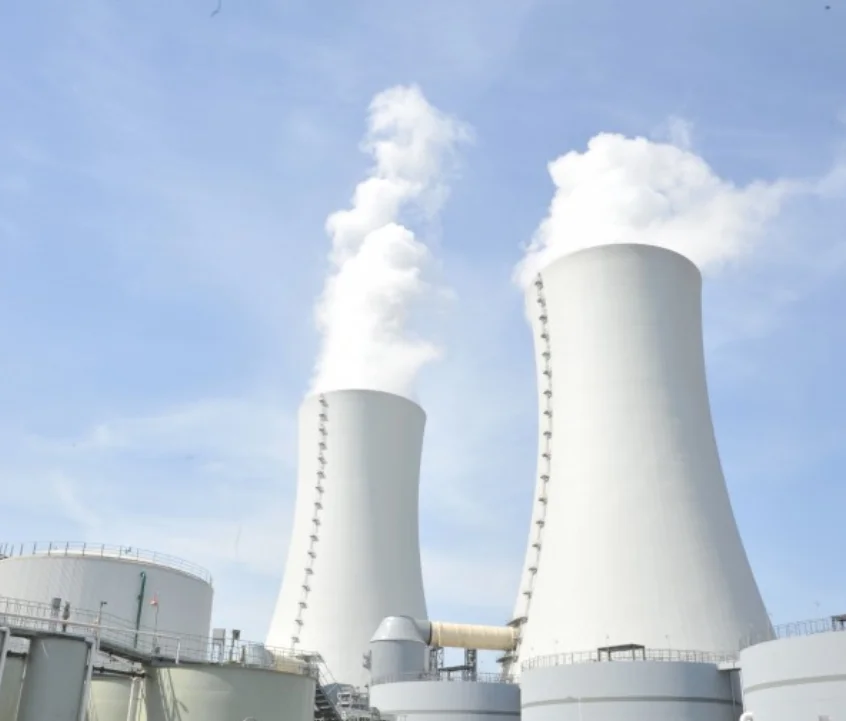
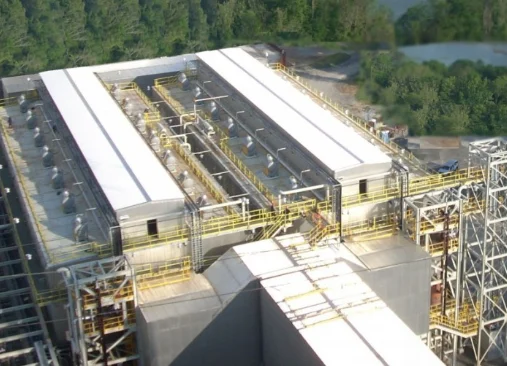
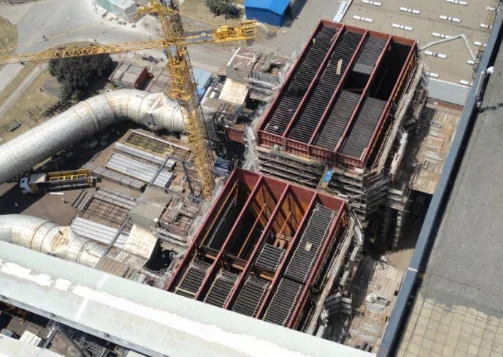
Packing & Delivery
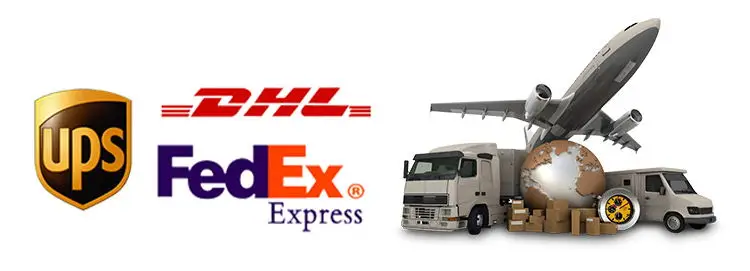
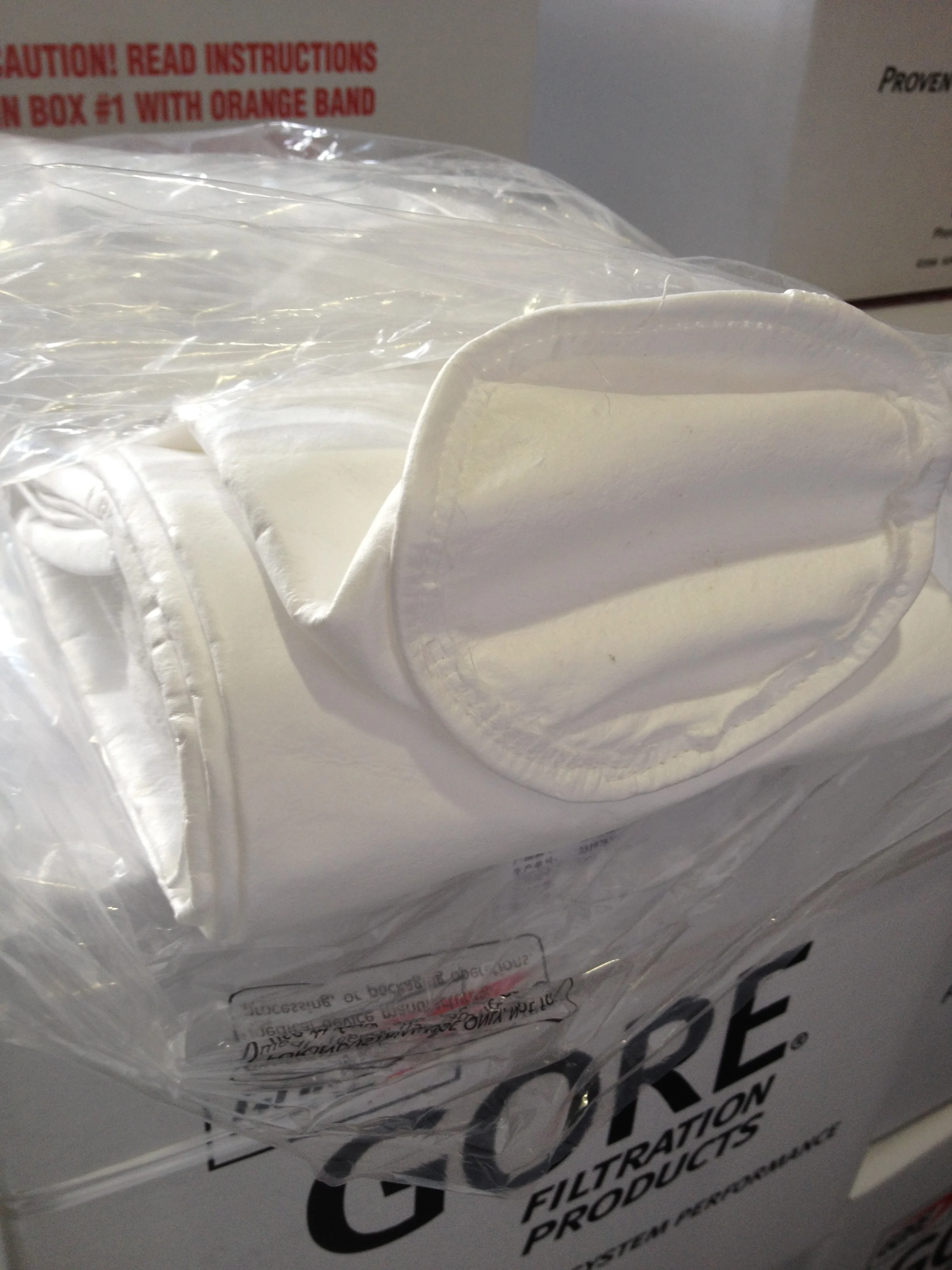
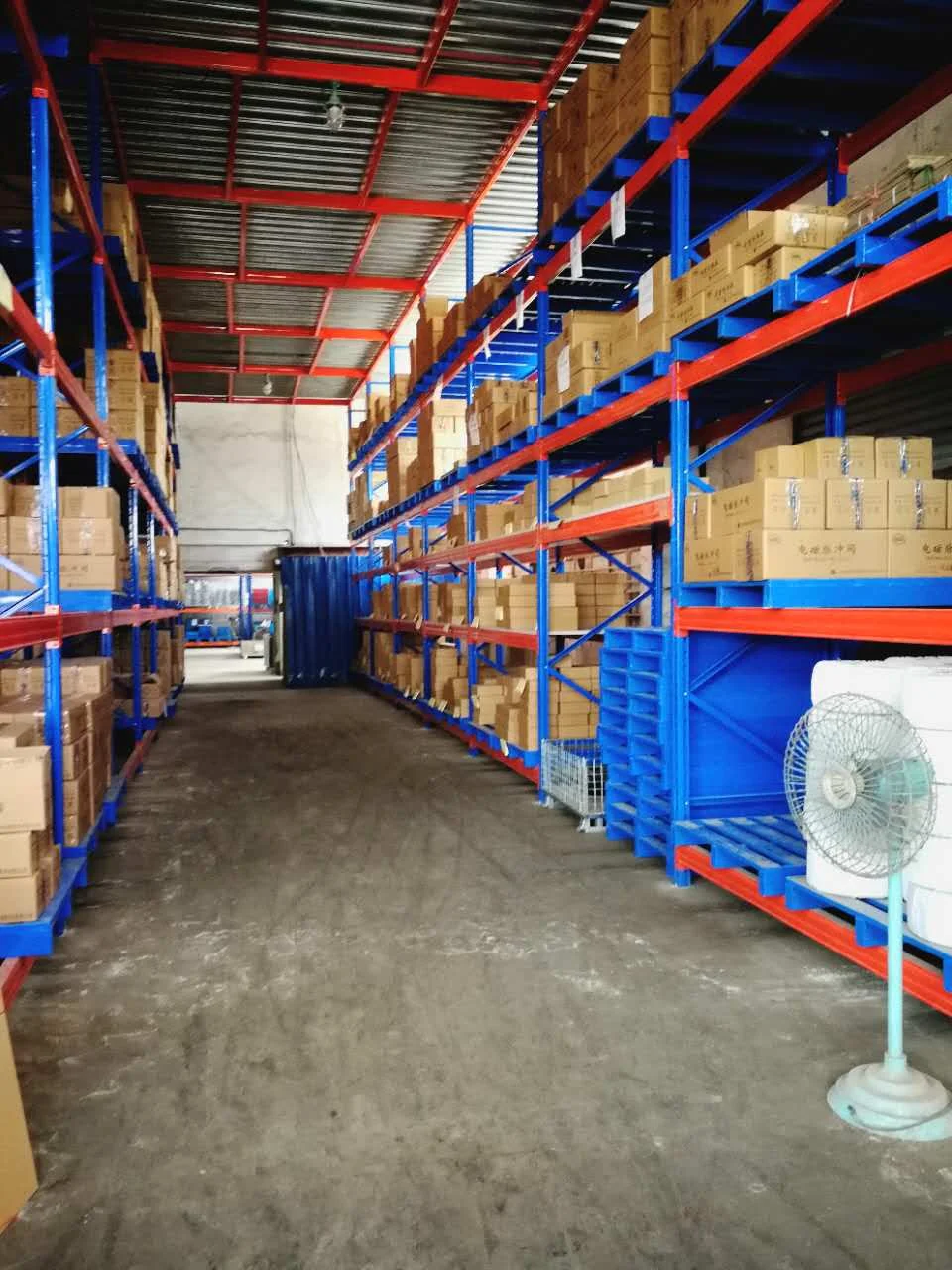
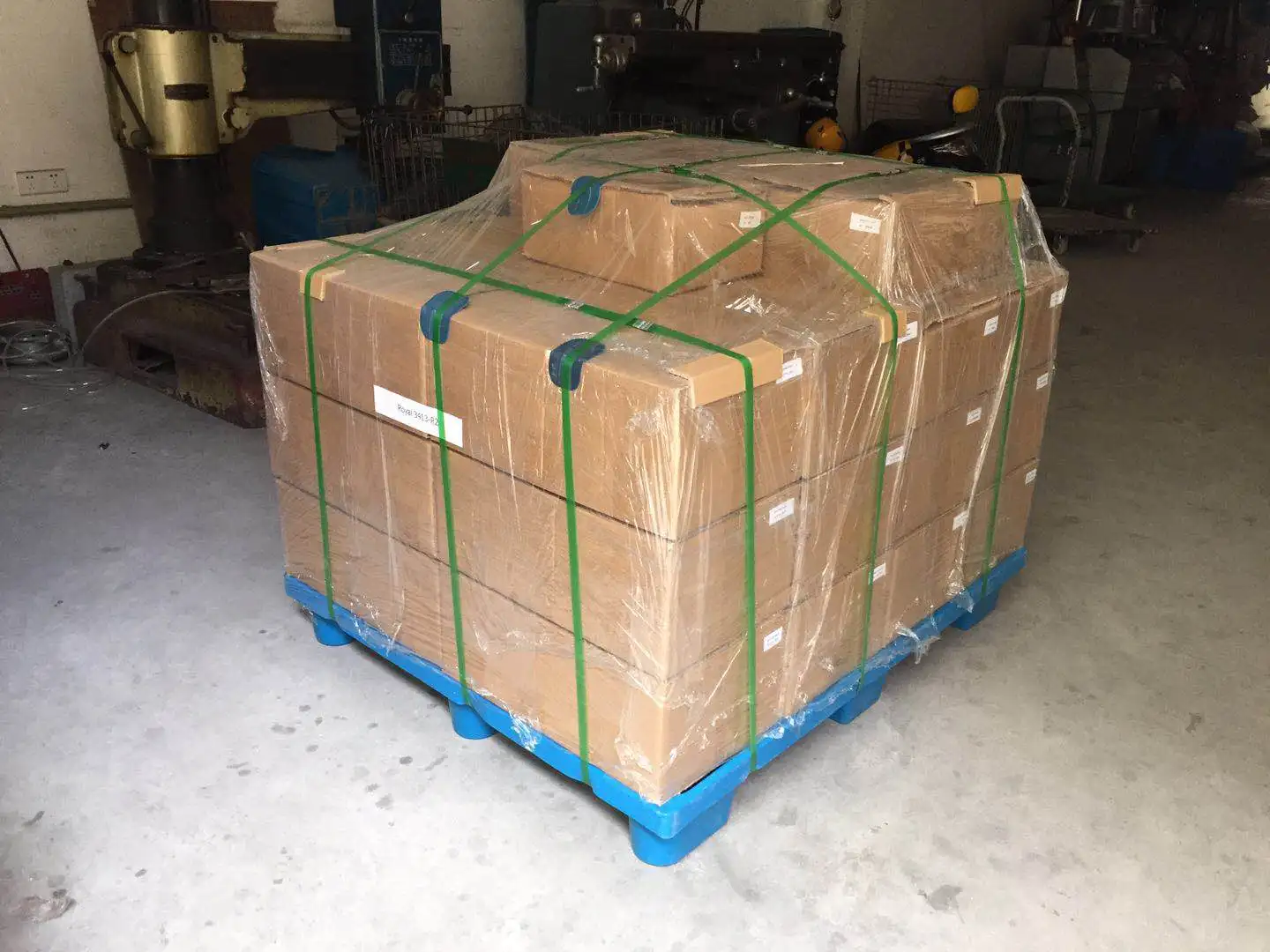
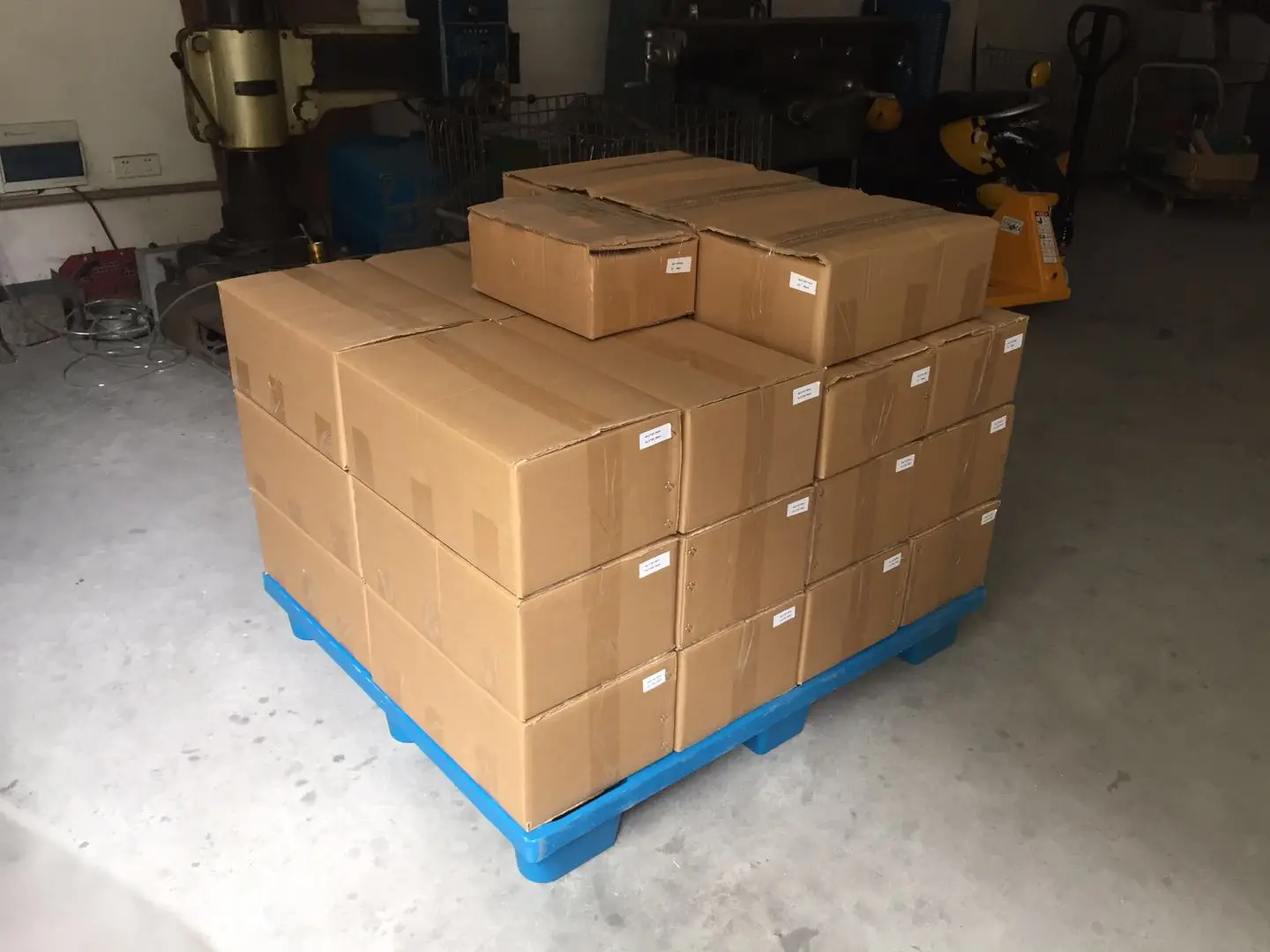
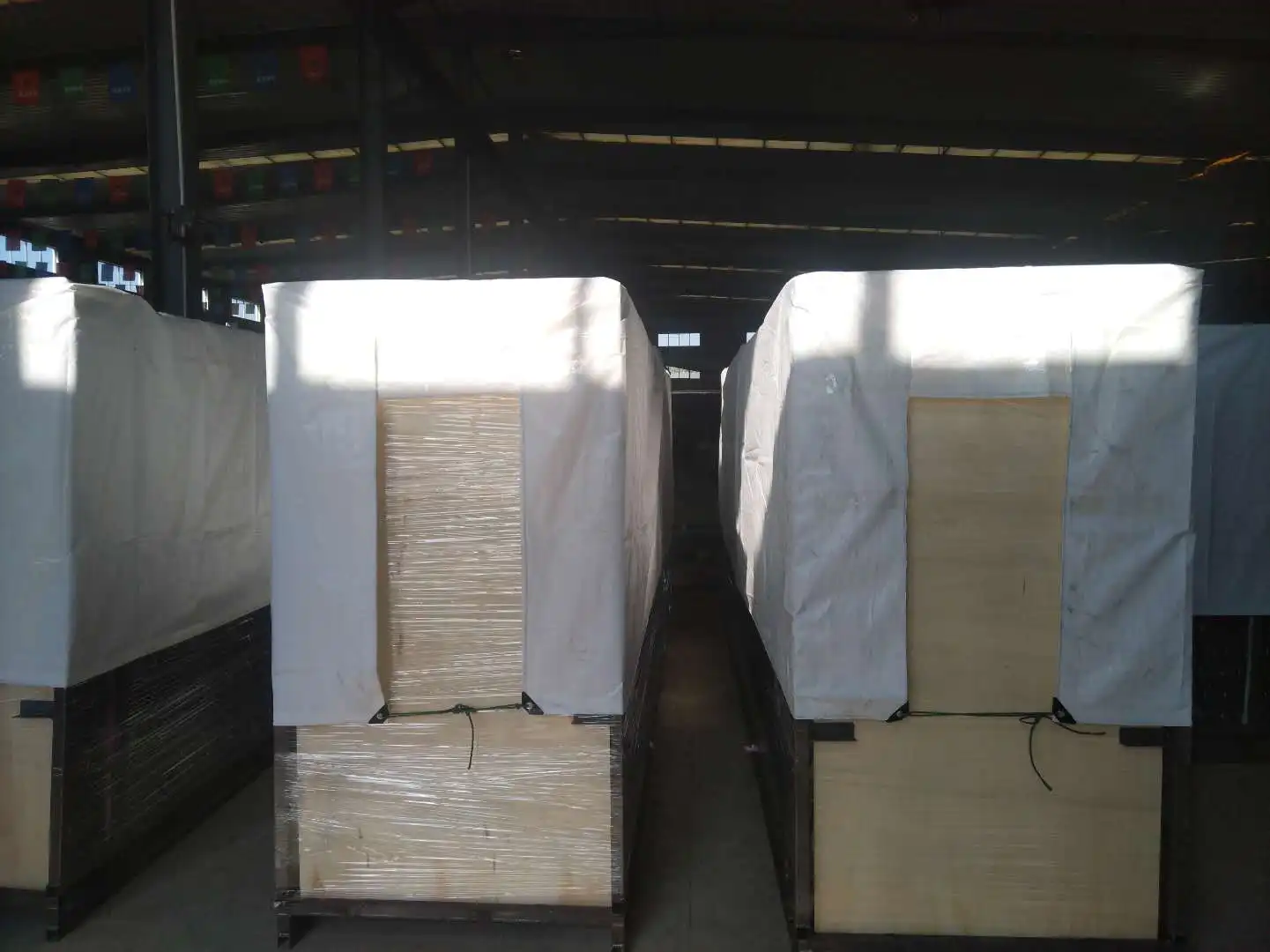
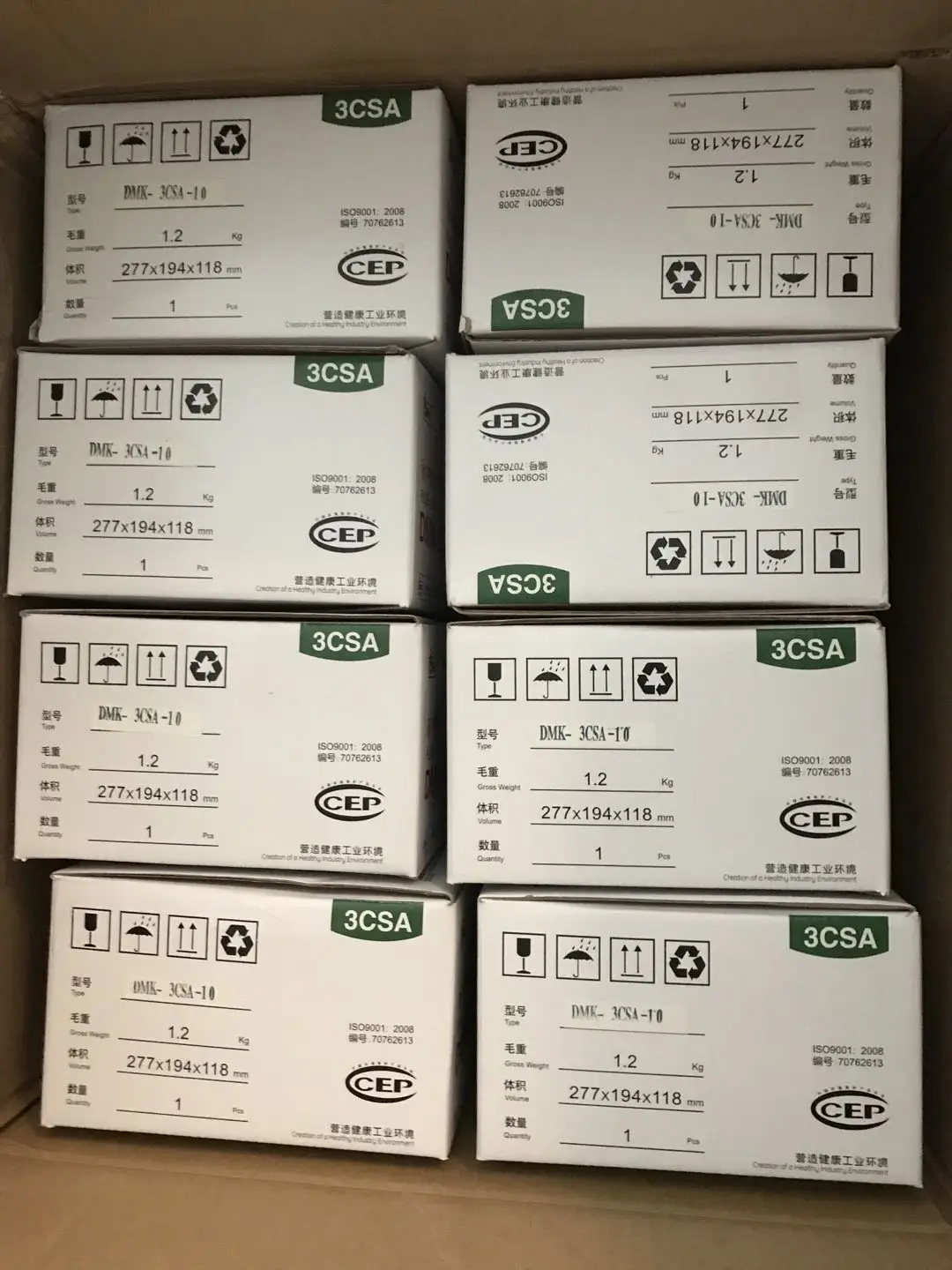
FAQ
Q:WHICH BAGHOUSE HOPPER DISCHARGE METHOD IS BEST?
A:Many problems arise over how to properly dispose of dust in the baghouse once it is collected. Improper dust disposal can directly impact the operation of your baghouse. Storing dust in your baghouse hopper is a terrible idea. Dust collector hoppers are designed for temporary storage only. If collected dust builds up in the hopper it can cause several problems,such as filter bag abrasion. However, this does not mean that all discharge methods work for all baghouses. As outlined above, serious problems arise when the baghouse hopper discharge system is not adequate to the dust loads passing through the unit. Additionally, the disposal methods may require more man power than available at the plant and lead to spillage and other issues.
The best method of hopper discharge varies from application to application and from unit to unit.
Q: What is “normal” differential pressure in a baghouse?
A:In most applications a baghouse dust collector should run between between 3″ to 6″ w.g. under normal use. Once levels rise above 6″ (roughly) and the cleaning system cannot return it any lower (even when turned to continuous cleaning or “Test” mode) it is a sign that the filters are beginning to be blinded and likely need to be changed. It is not advisable to run a baghouse with a DP higher than 6″ for any length of time as this will have an impact on the function of the entire system. Running at such a high DP will lead to a number of problems including vacuum loss at the pickup points of the system (loss of suction), lower air speeds in the ductwork, higher emissions, and higher energy usage.
If you are seeing levels below 3″ after having run the baghouse for sometime you liking are getting false DP readings. When brand new bags are installed in a dust collector they should provide approximately 1″ of resistance alone. Once they begin to load dust that number will rise to between 2″ – 3″ no matter how much you clean them.
A clean on demand baghouse controller (i.e. clean on pressure) is the best way to keep a dust collector running in the recommended DP range. (see article: 3 Cheap Ways to Increase Efficiency in Dust Collection Systems)
Q:How long will my bag-filters last?
A:Bag- filters have an average service life of 1-3 years in most applications. Some can go beyond that without major increases emissions, while others may last less than a year in more difficult applications. The main reason to replace baghouse filters is because when old they begin to leak and thus the system is no longer collecting particulates as its designed to do. Filters can also be damaged prematurely by sparks/embers that can cause fires or even explosions. Upset conditions in the process may cause a spike in temperature (beyond the maximum for the filter fabric) or may create an acid flash or similar chemical attack on the bags. Finally, bags may be damaged during maintenance or by other external forces.
The main signs that your filters need to be replaced are that they are can no longer be cleaned effectively by the baghouse and/or they start leaking.
Q:Can I Reuse My Baghouse Cages When I Change my Filters?
A:In many applications it is possible to reuse the cages once or possibly more. But in many other applications it may not be wise to reuse the cages.
Q:How pulsing valves work in a typical application for dust collector systems?
A:Pulse jet valves are used in filtering systems of dust collectors, gas turbines, and desulfurization equipment. They are commonly used to clean filters such as cartridge filters, envelope filters, ceramic filters, and sintered metal fiber filters.
Pulse jet valves are indirect operated solenoid valves especially designed for dust collector systems. When the solenoid is energized, trapped air above a diaphragm is quickly exhausted causing a high pressure difference across the diaphragm. Thereby the diaphragm is suddenly opened. When the solenoid is de-energized, air escapes through a hole to the chamber above the diaphragm which balances the pressure and instantly closes the valve.
Q:How to choose a correct pulsing valve ?
A:When we choose a correct pulsing valve, we normally need to check the main parameters that affect the selection.
Main parameters that affect the selection of pulse jet valves are as follows:
Tank volume: The amount of air volume stored in the supply tank which in turn depends on valve size.
Tank pressure: The air pressure in the tank which is also the inlet pressure of valve.
Max allowable pressure: Maximum line or system pressure for safe operation.
Electrical pulse length: The time during which the valve is energized.
Total pulse length: The time between when the valve opens and when it closes.
Peak pressure: The maximum pressure reached at the end of the blow pipe which creates the shock wave.
Pressure drop tank: The difference between the tank pressure before and after the shock wave. To maintain sonic flow in the blow pipes, it is necessary to limit pressure drop to a maximum of 50% of the absolute tank pressure. In an installation, it is the easiest way to reduce the electrical pulse time if the pressure drop is too high.
Performance ratio: The ratio between tank pressure and peak pressure in percentage. The amount of this parameter depends on the kV of the valve and the opening time.
Volume per pulse: The volume of air at atmospheric pressure passing through the valve per pulse. The greater this parameter, the better filter bags are cleaned, and more bags can be cleaned per valve.
These types of solenoid valves come with different choice of material of construction namely of body and of seal material. All materials of construction have specific properties that make them suitable for different applications. It is essential to choose the appropriate body and seal material for your media.
VIEW MORE
YOU MAY LIKE